Home > Company News > Properties, Processes and Applications of Silicone Materials
Company News
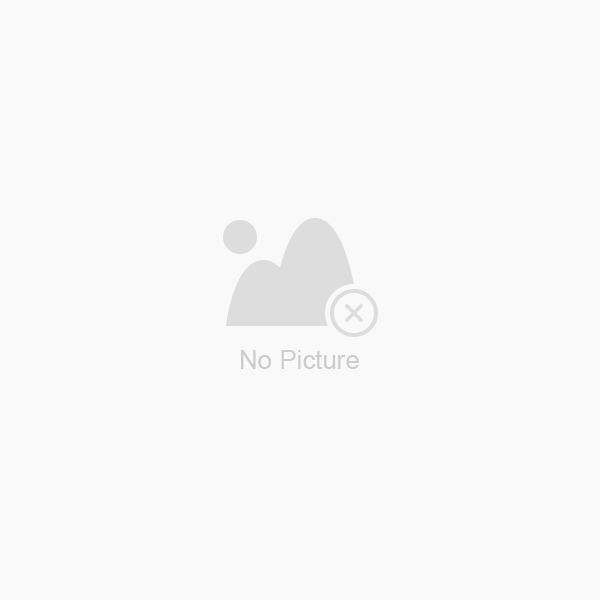
Silica gel material has the characteristics of high adsorption performance, good thermal stability, stable chemical properties, and high mechanical strength, and is widely used in product design. And the material is modified to make special silica gel to meet the functional requirements of different products, such as luminous, negative ions, discoloration and other characteristics.
Introduction to Silicone
Silica gel is a highly active adsorption material, which is an amorphous substance, which contains polysiloxane, silicone oil, white carbon black (silicon dioxide), coupling agent and filler, etc. The main component is silicon dioxide. It is insoluble in water and any solvent, non-toxic and tasteless, chemically stable, and does not react with any substances except strong alkali and hydrofluoric acid. Various types of silica gel form different microporous structures due to different manufacturing methods. The chemical composition and physical structure of silica gel determine that it has many characteristics that are difficult to replace by other similar materials: high adsorption performance, good thermal stability, stable chemical properties, and high mechanical strength.
Classification of silicone
Silicone can be classified according to various characteristics:
According to the composition, it can be divided into: one-component and two-component silica gel.
According to the vulcanization temperature, it can be divided into: high temperature vulcanization and room temperature vulcanization silica gel.
According to the form of the product, it can be divided into: liquid and solid silica gel.
According to the vulcanization reaction, it can be divided into: condensation reaction type, platinum addition reaction type and peroxide curing type.
According to the main chain structure, it can be divided into: pure silica gel and modified silica gel.
According to the product characteristics, it can be divided into: high and low temperature resistance type, antistatic type, oil and solvent resistance type, conductive type, foam sponge type, high strength tear resistance type, flame retardant and fireproof type, low compression deformation type, etc.
8 reasons why silicone is the best material for medical device design
1. Silicon-oxygen backbone can provide excellent thermal stability
Silicone has excellent thermal stability, allowing the device to maintain key performance even after sterilization. Silicones can be sterilized by high temperature steam sterilization, ethylene oxide sterilization (EtO) or gamma radiation.
2. Silica gel is an inert material
Silicones are generally inert to bodily fluids and medications, and have no odor. The chemical structure of silicones complies with USP Class VI and ISO 10993 standards.
3. Silica gel does not contain plasticizers or other organic additives
Plasticizers or other organic additives can negatively affect the delivered drug and, if present, have the potential to migrate into the drug solution. Silicone, on the other hand, contains no additives such as plasticizers or organic additives.
4. Silicone is durable
Silicone has good elasticity and recovery after puncture to reduce material fatigue. These key properties give silicone a long service life, even under dynamic stress.
5. Silicone has a low modulus
Silicone requires minimal insertion force to improve smooth operation of the device - or easier assembly when combined with other components.
6. Silicone can be formulated into various hardnesses
Silicone can be molded to a variety of hardnesses to accommodate either too hard or too soft materials, increasing the potential for improved ergonomics and comfort.
7. Silicone has a good design aesthetic
Many silicone elastomers are inherently transparent and readily colorable.
8. Silicone is easy to process
In addition to the comfort of hardness and aesthetics, silicone also offers a range of customization options. Materials can be applied to a variety of devices and designs, from infusion-type catheters to incision valves to breathing masks and more. Other customizable options include tensile strength, coefficient of friction, cure time and elongation.
Silicone processing technology
1. Molding
The molding process is mainly a production process formed by pressing molds in related machines, such as the production of silicone mobile phone cases, silicone ice trays, etc. The main production process is the silicone processing of silicone raw materials or rubber raw materials that are formed into products by heating and pressurizing in a closed mold cavity. Usually, the raw materials are uniformly mixed into a mixed rubber through a mixer, and the mold is moved into the vulcanization molding machine. Then the mold is closed and pressurized to form and solidify or vulcanize, and then demolded to obtain silicone products. This process is suitable for the processing of thermosetting materials.
2. Injection
This process requires relatively high quality, and is a combination of liquid silicone and plastic. Its products show good thermal stability, cold resistance, excellent electrical insulation properties, and no toxic substances are produced when burning. Therefore, it has become an irreplaceable material in the production design of health products, automobiles, baby products, medical products, diving products, kitchen utensils and seals.
3. Extrusion
Extrusion molding, extruded silicone products are usually formed by extruding silica gel through an extrusion machine. Generally, the shape of extruded silica gel is long, and the tubular shape can be cut at will. The shape of the extruded products is relatively simple, mostly strips. . Silicone tubes are widely used in the fields of medical and mechanical equipment. It can also be used as a buffer in the packaging material.
4. Calendering
The silicone rubber is kneaded and kneaded by adding silica, silicone oil, etc. to make a mixed rubber, and then the sheet is calendered. The film produced by calendering has obvious difference in physical and mechanical properties in the longitudinal direction and the transverse direction. This phenomenon is called the calendering effect. The specific performance is that the longitudinal tensile strength of the film is greater than the transverse direction, the transverse elongation at break of the film is greater than the longitudinal direction, and the longitudinal shrinkage rate of the film is greater than the transverse direction. The calendering effect is the result of the orientation of macromolecules and needle-like and flake-like compounds in the rubber compound along the calendering direction during the calendering process. The size of the calendering effect is related to the composition of the rubber compound, the calendering temperature, the speed, and the speed ratio. For larger products, such as silicone sheets, silicone plates.
5. Perfusion
The operation method of filling or pouring mold: pouring mold or pouring mold is used for relatively smooth or simple products, no mold line saves manpower and time, i.e. the product or model you want to reproduce is surrounded by rubber or glass plates, through vacuum pump The outgoing silica gel is poured directly into the product. After the silica gel is dried and formed, the product is taken out to form a mold (Note: The perfusion mold is generally made of silica gel with relatively soft hardness, so that it is easier to demould and will not damage the products in the silicone mold). It belongs to solid-liquid combination and is used in mobile phone sets, luggage sets and other products.
6. Coating
Fast vulcanization; strong adhesion; good fluidity and easy defoaming. The catalyst of platinum complex is non-toxic and tasteless, and has good air permeability, heat resistance and certain tensile strength after molding (use temperature -60℃~200℃). Excellent non-slip properties; no pollution; low hardness; strong adhesion. High tear; high transparency; good tensile properties. Wear resistance, washing resistance, high temperature resistance; high three-dimensional level, smooth, soft, good elasticity. Resistant to water washing and dry cleaning. Suitable for fabrics, with anti-aging effect, such as silicone gloves, rain boots, etc.
Application of Silicone in Medical Devices
Devices that come into contact with human skin:
(1) Respiratory mask: especially the mask that needs to be worn for a long time.
(2) Wound care: Silicone gel is more skin-friendly and breathable, and will not cause secondary damage to the wound. Therefore, Momentive Silicone Gel is an excellent choice for foam applications, scar patches, etc.
(3) Instrument handle: For medical instruments that need to be grasped, such as surgical knives, a soft and non-slip handle is a must.
Devices that come into contact with human orifices:
Laryngeal mask: In contact with the trachea, the silicone is soft and strong to keep the airway open.
Catheter: Silicone support produces a soft tube body, as well as a high tensile strength balloon.
Gastric tube: suitable hardness, silicone gastric tube is a good choice for patients.
Devices that come into contact with human blood and body fluids:
The catheter of the infusion device: such as the peristaltic pump tube of the infusion pump, the outer tube of the insertion type catheter.
Parts of infusion equipment: such as rubber plugs for needleless connectors, O-rings for kidney dialysis filters, etc.
Rubber plugs and hemostatic valves in various medical consumables that come into contact with medicinal liquids.
In addition, silica gel has a wide range of applications, from contact lenses to wearable medical testing equipment, from biopharmaceuticals to vaccine research and development, all of which are areas where silica gel can be widely used.
-
Inflatable rubber dam,Filling dam
-
Advantages of Movable Simplified Elevated Dam
-
Water-swelling rubber waterstop strip product type 20*30 caulking seal waterproof putty rubber waterstop strip
-
nflatable Rubber Water Dam Supplier
-
Ship Rubber Airbag Launching Marine Air Bag Price
-
Changhe Water Conservancy Project hydraulic steel dam water barrier dam bottom shaft dam drive lifting landscape gate
-
PVC tarpaulin custom color size portable water-filled inflatable temporary dam flood control pipe
-
Fast Dispatch Liquid Rubber Dam Inflatable Water Filled Rubber Dam For River
-
Water Stopper Rubber Waterstop Sealing water stops Belt Supplier
-
Hydraulic lift dam,Hydraulic lifting dam
-
Customized Hydraulic Elevator Dam,vanishing dam
-
PVC tarpaulin custom color size portable water-filled inflatable temporary dam flood control pipe
-
inflatable rubber dam
-
Rivers store, fill, Inflatable rubber dam china rubber dam
-
Inflatable, water-filled rubber dam, rubber barrier, sight dam
-
River dam construction rubber dam inflatable rubber dam
-
Gas Shield Dam, gas shield gate, gas shield rubber dam
-
Rubber stopper Waterstop Seal Expansion Strip
-
Hydraulic Elevator Dam Hydraulic lifting dam
-
Water filled inflatable rubber dam,River rubber dam
-
Pneumatic Marine Parts Underwater Air Lifting Bags for Ship Landing and Launching
-
Expanding Rubber Waterstop for Construction Concrete Leak Proof
-
Air Water Inflatable Rubber Dams
-
Rubber waterstop embedded rubber waterstop external steel edge